Topics
Gunite Pool Construction
Gunite Design Basics
Swimming Pool Cost & Pricing
Swimming Pool Loans & Financing
Inground Spas/Gunite Spas
Backyard-Space Considerations
Swimming Pool Shapes, Dimensions, Depths
Pool Building Materials
Gunite pool construction
What is the process for building a gunite pool? (concrete / shotcrete)
Gunite pool construction involves multiple phases. After planning and designing the pool, these steps typically include: permitting, layout, excavation, steel installation, plumbing, electric, gunite application, installation of tile and coping, deck installation, plaster/interior finish, and start-up.
The sequence here may vary based on local building codes and practices, as well as if the project contains any specialized custom design features.
How long does it take to build a gunite pool?
What underground obstacles can pose challenges to inground pool construction?
How do soil conditions affect inground pool construction?
How do inground pool builders address special soil conditions for gunite pools?
Gunite Design Basics
What is a gunite swimming pool? (concrete / shotcrete)
A gunite pool is built with a concrete blend that consists of sand, cement, and water. (Shotcrete is a similar blend, but also contains pea gravel.)
Construction crews spray the material through a high-pressure air hose onto a reinforcing network of steel bars to form a thick, rock-hard pool shell.
Both gunite and shotcrete pools are engineered concrete creations that provides superb design flexibility and lasting durability.
Learn more about construction elements of a gunite pool: 5 Key Construction Terms for Concrete Designs
What are the benefits of a gunite swimming pool?
What happens during an in-home inground pool estimate?
Swimming Pool Cost & Pricing
How much does an inground gunite pool cost? (concrete / shotcrete)
Because gunite pools are custom projects—each with unique specifications and site conditions, and built with materials and craftsmen that vary by markets around the country—it’s very difficult to cite an average cost.
One major consideration will be whether or not the project includes a spa. This popular feature may add around 15 to 25 percent of the cost of the basic pool.
Other determining factors that affect the final price include size (often measured in perimeter feet), depth, shape, design elements, functional features, equipment and technology options (e.g., pool automation), material choices, accessories (e.g., a pool slide), local construction costs, local labor costs, and specific backyard building conditions.
By speaking to local pool builders and providing some general specifications, you will develop a sense for the typical starting pool prices in your area.
Learn more:
3 Reasons Swimming Pool Builders Should Never Cut Corners
Affordable Custom Pool Style
What backyard conditions increase inground pool construction costs?
Swimming Pool Loans & Financing
Is swimming pool financing available? How can I get a pool loan?
Yes, sources are available for pool loans, and some pool builders help arrange pool financing for buyers.
Blue Haven offices draw on a national network of home-improvement lenders to help clients obtain financing (on approved credit). Programs vary state by state, and lenders have different underwriting criteria.
How do I know if I will qualify for a pool loan?
Inground Spas/Gunite Spas
Should I include a spa with my inground swimming pool? (gunite / concrete / shotcrete)
Gunite spas are custom builds that are popular among pool buyers because they serve as a lovely focal point in the pool and offer so many health and lifestyle benefits.
Particularly when the spa is elevated, its façade and spillway provide superb design opportunities and also serve as a distinctive water feature.
Beyond its beauty, a spa brings added value to your lifestyle. It’s an ideal amenity for unwinding mentally and physically, offering warm hydrotherapy for sore muscles, a place for low-impact exercise, support for enhancing blood circulation, promotion of better sleep patterns, general relaxation and serenity, and a setting for socializing and conversation.
This feature also provides a fun spot to hang out or play—even when it’s cooler at night or after swim season ends. Learn more about gunite spas and design ideas: Custom Inground Spas
What inground spa shapes are most popular?
What shape of inground spa should I choose?
How much cost will a spa add to my inground pool budget?
I don’t want a pool or don’t have room for one. Can I get a custom gunite spa only?
Backyard Space/Considerations
How much backyard space do I need for an inground pool?
Depending on the backyard configuration, you will likely need a rough minimum of 500 square feet for an inground pool.
However, the final minimum number will vary with the shape of the property. That’s because gunite pools allow builders to develop shrewd designs to maximize use of available space.
Enormous versatility for pool size and shape is possible. A builder may even configure a pool that will use space from both your backyard and side yard.
Other factors may enter the equation and influence how much backyard space you can use and where the pool may be positioned. One is building codes, which vary by city. For example, most codes require pools to be 3 to 5 feet away from the house and the property line.
Keep in mind, you will need some area around the pool for decking. You may want to include other backyard features as well. Your builder will advise you of other considerations—as well as opportunities—for space-saving design solutions.
Learn more about pool planning: Pool Design Dimensions: 3 Key Initial Questions to Ask
Can I build an inground pool in a small backyard? Will a gunite pool fit in my backyard?
What kind of backyard access do I need to build an inground pool?
Swimming Pool Shapes, Dimensions, Depths
What size inground pool should I get for a gunite pool? (concrete / shotcrete)
Along with your builder, you can determine a gunite pool size by considering available backyard space, desired pool shape, pool style, features, accessories, and plans for any outdoor amenities.
How your family plans to use a pool is also important: For example, if you want a pool for swimming laps or a pool with a diving board, a minimum length is typically required. Likewise, including a beach entry and a big custom spa for a family of six will dictate a specific length/depth requirements.
On the other hand, if you just want to jump in the water to cool off, a compact splash pool will suffice.
You can learn more here about planning pool size:
Swimming Pool Design Dimensions: 3 Key Initial Questions to Ask
Concrete Pools Ensure Best Versatility for Size Shape & Configuration
What are the most popular shapes for a gunite pool?
What are the most space-efficient shapes for an inground pool?
What’s a “sports pool”? What’s a “play pool”?
Building Materials
What is used to make inground pools?
Three kinds of materials are used to produce in-ground pools: vinyl liner, fiberglass, and gunite (concrete/shotcrete).
What is gunite? How is it used to build pools?
What is shotcrete? How is it used to build pools?
What is pool plaster? What’s its purpose?
What kinds of pool plaster are available? What are my options for pool finishes?
What is marcite pool plaster finish?
What is ColorQuartz® pool plaster finish?
What are the benefits of a ColorQuartz® pool finish?
What is pebble pool plaster finish?
What are the benefits of a pebble pool finish?
What material is used to make inground pool steps?
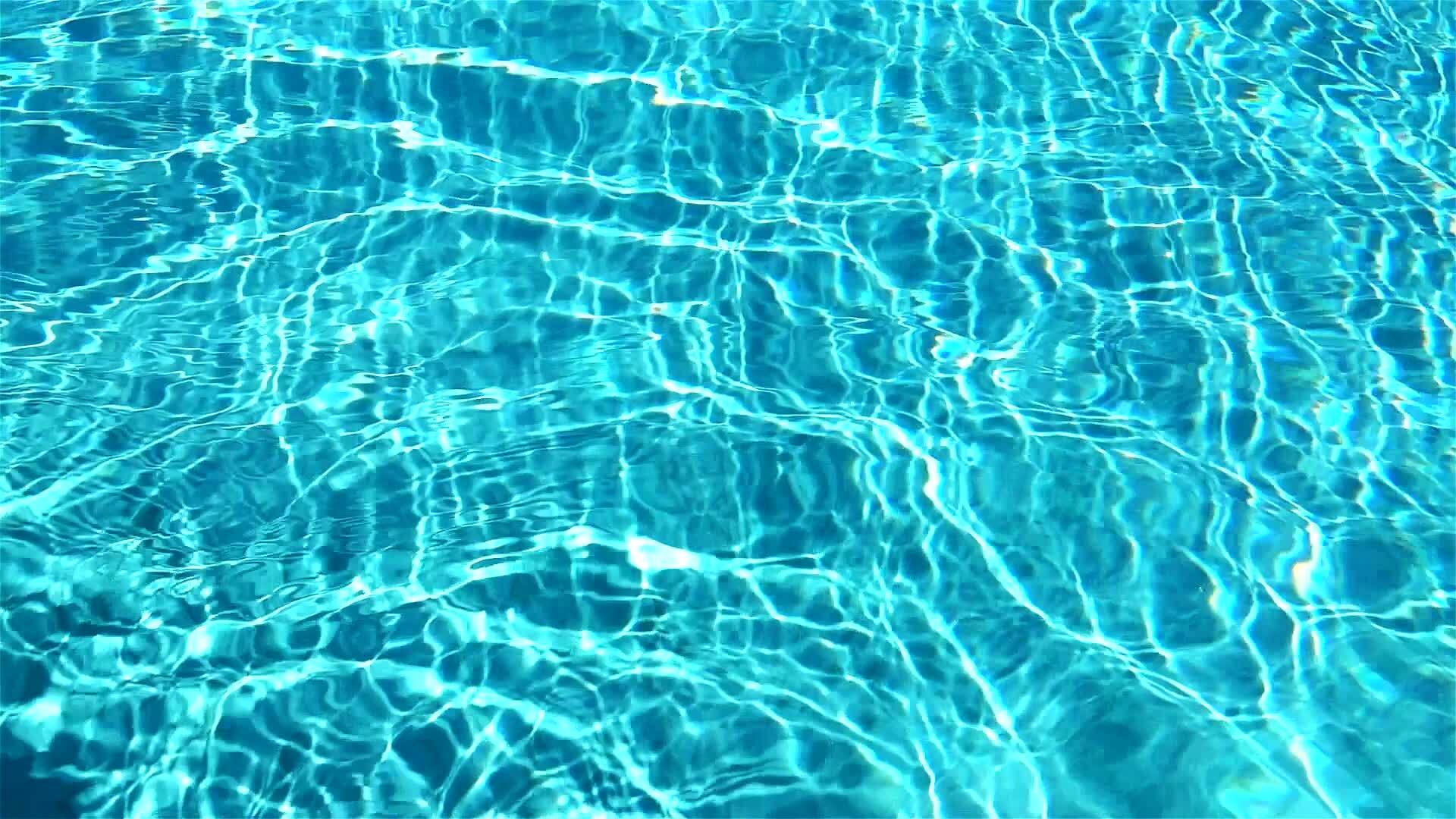